IV Pump Maintenance: How to Properly Clean Infusion Systems
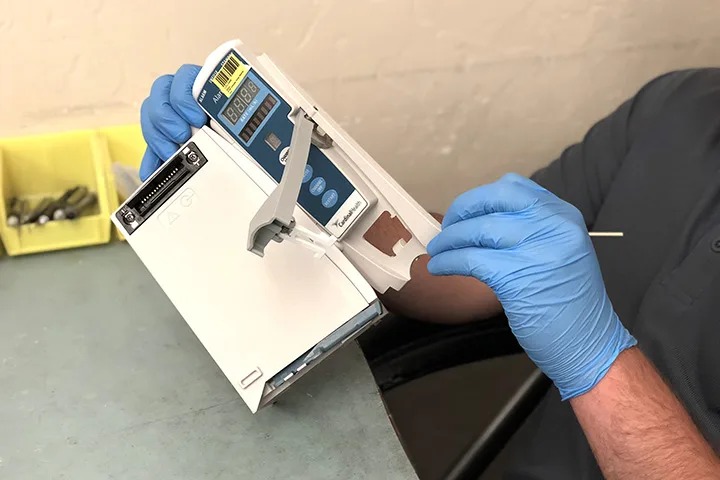
For all kinds of healthcare facilities, IV infusion pumps are a patient essential. In fact, according to the Materiel Services department at the University of Michigan Health Systems, 86% of all patients admitted to hospital beds require infusion pumps. Syringe pumps and smart pumps are used in both medical centers and by patients in their own homes. But to keep these infusion systems working properly and keep patient health from being compromised, specific care and cleaning instructions must be followed. The following are some of those instructions.
Cleaning Before Use
Infusion system manufacturer will outline specific cleaning and disinfecting protocol for their syringe infusion pumps and other infusion equipment. Be sure to use only approved disinfecting chemicals and cleaning solutions for this purpose. In some cases, a two-step cleaning process may be necessary.
Don't forget to clean not only the areas used during infusion but also the pump's stand and wheels. These surfaces can be sensitive to non-approved chemicals, so you must use the correct cleaning agents approved by both the manufacturer and the Environmental Protective Agency. Staff members should focus on the pump's wheels, in particular, as they are prone to picking up dust. Even if you've followed all recommended cleaning procedures for the device itself, dusty wheels can give a poor impression to patients. To minimize this, you can cover these pumps when not in use.
It's important that you prioritize staff member training that includes these procedures. You may need to unplug the device during certain cleaning procedures. You must also make sure these syringe infusion pumps are in good working order between patient use.
Cleaning After Use
Proper cleaning after infusion pump use will ensure compliance and safety for both patients and employees. By following instructions provided by pump manufacturers, you can prevent exposure to bodily fluids, blood, and/or chemical agents.
As a rule, the hospital staff should always remove organic debris before disinfecting these devices. Cleaning these pumps during use can help to ensure compliance. To streamline this process, you can check whether the manufacturer recommends disposable disinfecting wipes or whether you can purchase a button overlay to make cleaning easier.
After the pump is no longer in use, a designated staff member should bring the device from the bedside to a storage room or a cleaning area. To make certain proper procedures are being followed, this responsibility needs to be outlined clearly. Follow a specific cleaning and disinfecting process as outlined by the manufacturer, taking care to make special accommodations for organisms that are more difficult to kill (like Norovirus).
Creating a Maintenance Policy
Facilities will find compliance is easier to come by if they create a specific maintenance policy for their infusion systems and track that these processes are actually being done. These procedures must ensure that pumps are disinfected, in good working order (which includes following lubrication recommendations), and ready to be used at any given time. Many facilities have embraced electronic tracking systems, which leave less room for error. But some still employ a manual tracking system. No matter what, it's vital to address who is charged with cleaning, disinfecting, and maintaining these devices and how these procedures are accomplished. If a device is in need of repairs, it must be "quarantined" to ensure it will not be used or changed in any way until it's cleared.
Considering that IV pumps are a crucial component of your facility, keeping them maintained must be high on your list of priorities. Of course, creating an outstanding patient experience starts with investing in the best equipment possible. To find out more about our medical equipment rentals and the types of infusion systems we carry, please contact us today.